PLC Basics: Introduction to Programmable Logic Controllers
Programmable Logic Controllers (PLCs) automate electromechanical processes that industries widely use to control and monitor manufacturing processes, such as assembly lines, robotic devices, and other machinery. PLCs have become an indispensable tool in modern industrial automation, and understanding their basics is crucial for anyone who wants to work in the field of automation. In this article, we will cover the basics of PLCs, including their history, operation, and applications.
Introduction
Specialized computers called PLCs control and monitor industrial processes by automating complex and repetitive tasks, replacing traditional electromechanical systems. Their programmable nature allows for easy Introduction to Programmable Logic Controllers, to perform different tasks without the need for physical modification of the hardware.
History of PLCs
The concept of PLCs was first introduced in the late 1960s by Richard Morley, an engineer at General Motors. The first PLC was called the Modicon 084, which was used to replace the hard-wired relay systems in automobile manufacturing plants. PLCs quickly gained popularity due to their flexibility, ease of use, and cost-effectiveness.
Components of a PLC
A typical PLC consists of the following components:
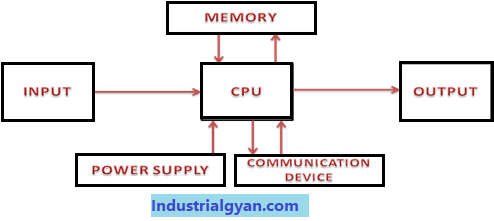
- Processor Unit: This is the brain of the PLC, which processes the inputs and outputs and executes the programmed instructions.
- Input Module: This module receives signals from sensors, switches, and other devices and converts them into digital signals that can be processed by the PLC.
- Output Module: This module sends signals to actuators, motors, and other devices to control the operation of the system.
- Power Supply: This provides the required power to the PLC and its components.
- Programming Device: This device is used to create, modify, and download the PLC program to the processor unit.
Basic Operation of a PLC
The basic operation of a PLC involves the following steps:
- Input devices send signals to the PLC.
- The processor unit reads the input signals and executes the programmed instructions.
- The processor unit sends output signals to the output devices.
- The output devices perform their designated functions.
Types of PLCs
There are several types of PLCs available in the market, each designed for specific applications. Some of the common types of PLCs are:
- Modular PLCs
- Compact PLCs
- Rack-mounted PLCs
- Safety PLCs
- Distributed PLCs
Advantages and Disadvantages of PLCs
PLCs offer several advantages over traditional electromechanical systems, including:
- Flexibility: Users can easily reprogram PLCs to perform different tasks without the need for modifying the hardware.
- Reliability: PLCs provide higher reliability than traditional systems, as wear and tear do not affect them.
- Cost-effectiveness: PLCs are cheaper than traditional systems, as they require less wiring and components.
However, there are also some disadvantages to using PLCs, such as:
- Complexity: PLC programming can be complex and time-consuming.
- Maintenance: PLCs require regular maintenance to ensure their proper functioning.
- Security: PLCs are vulnerable to cyber threats, as they are connected to the internet.
Applications of PLCs
PLCs widely used in industries to control and monitor various processes, such as:
- Assembly lines
- Conveyor belts
- Robotics
- Packaging
follow us on LinkedIn

I am an electrical & automation engineer with extensive experience in Design, PLC programming, SCADA development, and IoT integration. I have a strong background in the industry, focusing on the Design & Development of Hardware, Software &Industry 4.0 technologies, and the integration of intelligent manufacturing systems.
I have a deep understanding of electrical principles and am proficient in various programming languages, including Ladder Logic, Structured Text, and Python. In addition, I have experience with various PLC, SCADA & IoT technologies and a track record of successful integration projects for various clients.