Lap Winding: An Essential Technique in Electric Motor Design
In the realm of electric motor design, various winding techniques are employed to ensure optimal performance and efficiency. One such technique is lap winding. In this article, snubber circuit we will delve into the intricacies of lap winding, exploring its purpose, advantages, and applications. From its fundamental principles to practical implementations, we will provide you with a comprehensive understanding of lap winding.
Table of Contents
- Introduction to Lap Windings
- The Working Principle of Lap Windings
- Advantages of Lap Windings
- Applications of Lap Windings
- Factors Affecting Lap Winding Design
- Step-by-Step Guide to Lap Windings
- Comparison with Other Winding Techniques
- Challenges and Considerations in Lap Windings
- Future Trends in Lap Windings Technology
- Conclusion
- Frequently Asked Questions (FAQs)
1. Introduction to Lap Winding
Lap windings are a common technique used in the construction of electric motors, particularly those with a large number of poles. It involves connecting the armature coils in a parallel manner, forming multiple paths for the current to flow through. By employing this winding method, the magnetic field generated within the motor can be efficiently utilized, resulting in enhanced performance and power output.
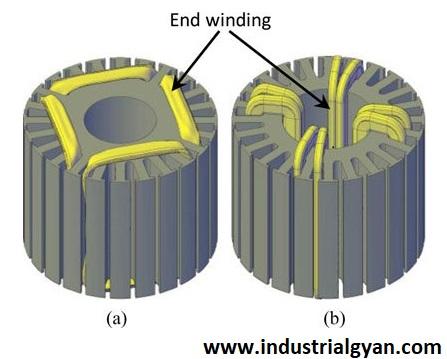
2. The Working Principle of Lap Windings
In lap windings, the end of each coil is connected to the beginning of the adjacent coil. This connection creates a series of closed loops, resembling laps, hence the name lap windings. The number of laps corresponds to the number of poles in the motor. When current is applied to the winding, it generates a magnetic field that interacts with the stator’s magnetic field, thereby inducing motion.
3. Advantages of Lap Winding
Lap winding offers several advantages in electric motor design:
i. Higher Current-Carrying Capacity
Due to its parallel connection scheme, lap windings allow for a higher current-carrying capacity compared to other winding techniques. This feature enables motors to handle larger electrical loads, vi characteristics of scr making lap winding particularly suitable for applications requiring high torque and power output.
ii. Improved Cooling Efficiency
The parallel connection of coils in lap winding facilitates the better heat dissipation. As the current is distributed across multiple paths, each coil experiences a lower current density, resulting in reduced heat generation. This enhanced cooling efficiency promotes motor longevity and reliability.
iii. Enhanced Commutation
Commutation is a crucial process in electric motors, involving the conversion of electrical energy to mechanical energy. Lap windings enhance commutation by minimizing the formation of sparks and reducing brush wear. This leads to improved motor efficiency and reduced maintenance requirements.
4. Applications of Lap Winding
Lap windings find wide-ranging applications in various industries. Some notable applications include:
i. Industrial Machinery
Lap-wound motors are commonly employed in heavy-duty industrial machinery such as compressors, pumps, and generators. The high current-carrying capacity and robust performance of lap-wound motors make them ideal for these demanding applications.
ii. Electric Vehicles
With the increasing popularity of electric vehicles (EVs), lap-wound motors have become a preferred choice for their propulsion systems. The efficiency and power capabilities of lap winding contribute to the overall performance and range of EVs.
iii. Renewable Energy Systems
Lap-wound generators are utilized in renewable energy systems such as wind turbines and hydroelectric power plants. The reliability and efficiency of lap-wound generators make them well-suited for harnessing renewable energy sources.
5. Factors Affecting Lap Windings Design
Several factors influence the design of lap winding in electric motors:
i. Number of Poles
The number of poles in the motor determines the number of laps required in the winding. A higher number of poles necessitates a greater number of coils and more complex winding configurations.
ii. Coil Pitch
Coil pitch refers to the distance between the beginning of one coil to the beginning of the next coil in the same lap. Determining the optimal coil pitch is essential for achieving balanced magnetic forces and reducing harmonic vibrations.
iii. Coil Span
Coil span is the distance between the two sides of a coil that are connected in parallel. Proper selection of coil span ensures uniform distribution of current and minimizes the risk of short circuits.
6. Step-by-Step Guide to Lap Windings
To implement lap winding effectively, follow these steps:
- Determine the number of poles required for the motor.
- Calculate the number of coils and laps based on the desired performance characteristics.
- Select the appropriate coil pitch and coil span.
- Arrange the coils in the winding configuration, connecting the end of one coil to the beginning of the next coil.
- Ensure proper insulation and secure the winding in place.
- Connect the winding to the power source and perform rigorous testing to validate its functionality.
7. Comparison with Other Winding Techniques
While lap windings offer numerous advantages, it is essential to consider other winding techniques and their suitability for specific applications. Some common winding techniques include wave winding, concentric winding, and distributed winding. Each technique possesses unique characteristics that make it suitable for particular motor designs and operational requirements.
8. Challenges and Considerations in Lap Windings
Despite its benefits, lap windings pose certain challenges and considerations:
i. Increased Complexity
Lap windings require intricate winding configurations, especially for motors with a high number of poles. This complexity can make manufacturing and assembly more challenging.
ii. Space Limitations
The parallel connection of coils in lap winding may consume more space compared to other winding techniques. This factor should be taken into account when designing compact motor systems.
iii. Skewing
To reduce harmonic vibrations and improve performance, skewing is often employed in lap-wound motors. Skewing refers to the intentional misalignment of stator slots or rotor laminations. The implementation of skewing adds an additional layer of complexity to the winding design.
9. Future Trends in Lap Windings Technology
The field of lap windings continues to evolve, driven by advancements in motor technology and emerging applications. Some potential future trends include:
- Integration of lap windings with advanced materials to enhance motor efficiency and reduce weight.
- Development of automated winding processes utilizing robotics and artificial intelligence.
- Optimization of lap winding configurations using computer simulations and modeling techniques.
10. Conclusion
Lap windings are a fundamental technique in electric motor design, offering advantages such as higher current-carrying capacity, improved cooling efficiency, and enhanced commutation. Its applications span industrial machinery, electric vehicles, and renewable energy systems. While lap windings present challenges and considerations, ongoing technological advancements are driving its further development. By understanding the principles and intricacies of lap windings, engineers and designers can harness their potential to create efficient and reliable electric motors.
Frequently Asked Questions (FAQs)
- What are lap windings?
Lap windings are a winding technique used in electric motor design, where the end of each coil is connected to the beginning of the adjacent coil in a parallel manner.
- What are the advantages of lap windings?
The Lap winding offers advantages such as higher current-carrying capacity, improved cooling efficiency, and enhanced commutation.
- Where is lap winding used?
It Lap windings find applications in industrial machinery, electric vehicles, and renewable energy systems.
- Are there any challenges in lap windings?
The Lap winding poses challenges such as increased complexity, space limitations, and the need for skewing to reduce harmonic vibrations.
- What are the future trends in lap windings technology?
Future trends in lap winding technology include the integration of advanced materials, automated winding processes, and optimization through computer simulations and modeling.
You can follow us on LinkedIn
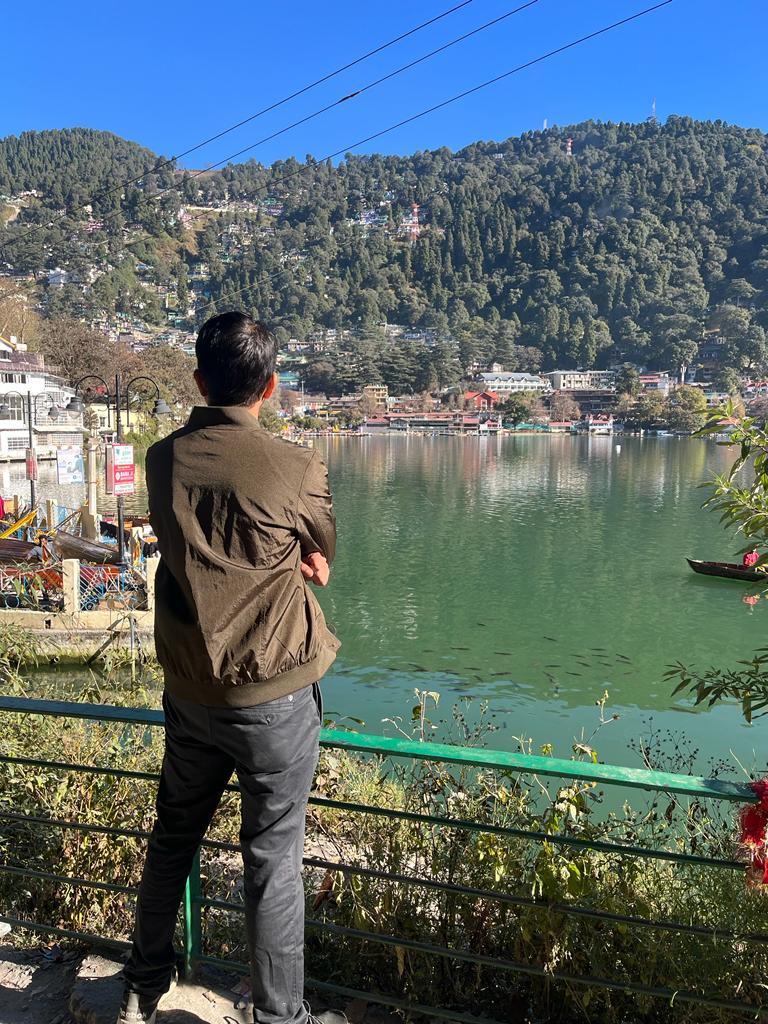
I am a highly motivated and skilled individual with a passion for Electrical engineering. I have 1 year of experience in Robotics and Electrical engineering, which has allowed me to develop a strong set of skills in PLC, Painting Robots, SCADA. I am a quick learner and am always looking for new challenges and opportunities to expand my knowledge and skills. I am a team player and enjoy working with others to achieve a common goal. Successfully completed many projects for a various clients in the automobile sector.
Thank You